Providing high-performance and customized gear machine tools, pursuing an unceasing technical and technological evolution, constantly enhancing their skills and know-how. These are the differentiating values on which Comur has founded its business and its growth path. These guidelines have led to the development of customized solutions, including gear hobbing and gear shaping machines, gears shaving and sharpening machines, together with other complementary equipment. Among them, stands out also a new line of hobbing machines, designed and manufactured in the Gaggio Montano (Bologna, Italy) plants.
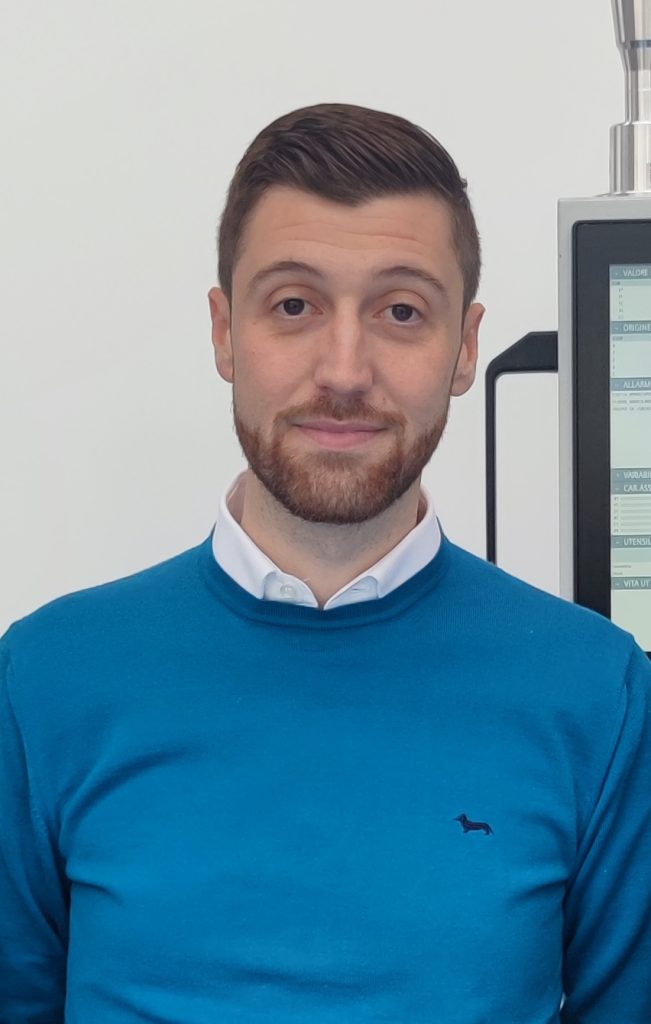
New design for new performances
As part of the product innovation, the new line of EVO hobbing machines represents a remarkable technological leap for Comur. «The machine structure – underlines the co-owner and sales manager, Mr. Matteo Tonelli – has been completely redesigned and, also at an aesthetic level, great attention has been paid to design. Going into more technical detail, some interesting characteristic elements then emerge, such as the asymmetric hobbing head. It makes it possible to carry out hobbing machining in presence of a very large diameter footprint, until now impossible on machines of this type. This peculiarity enables the implementation of hobbing with very small external diameter with very small external diameter, close to dimensions that can reach 600 mm in diameter. Also worth mentioning the ability to design workpiece clamping equipment with much larger diameters without risk of collision and, above all, without the need to unload and to weaken the equipment, thus greatly increasing the process rigidity. It is possible to carry out this hobbing by exploiting the whole shifting stroke of 300 mm».
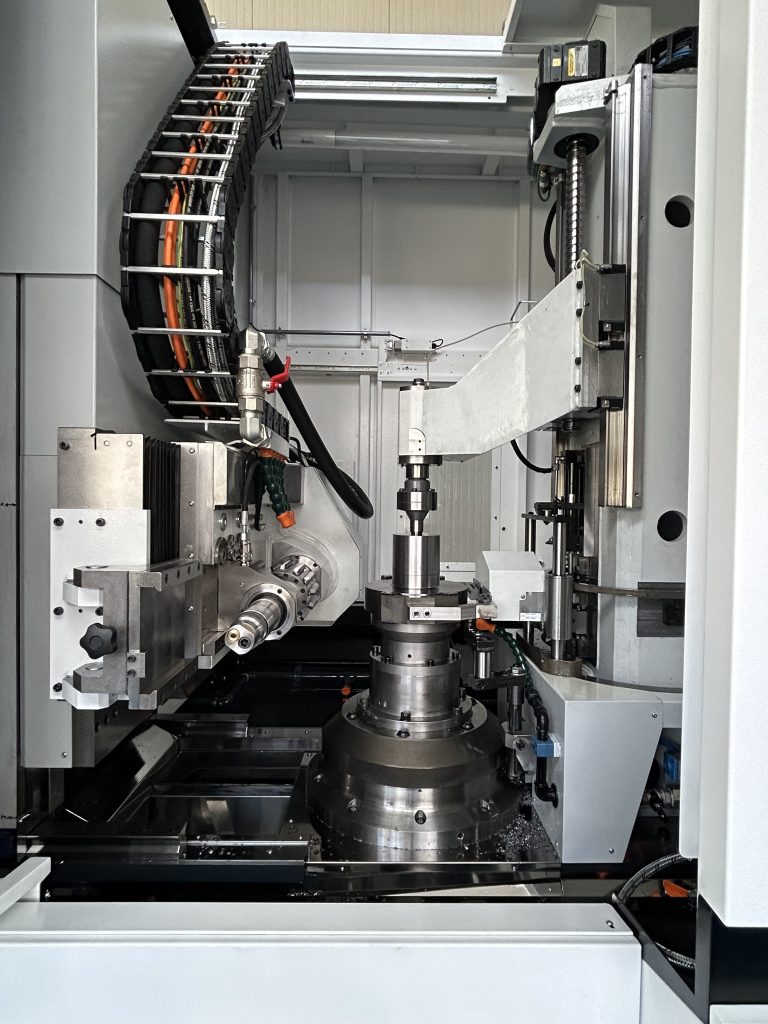
Uncompromised stiffness, reactivity and precision
Featuring a compact design, easy handling and quick installation, the new EVO 400 CNC hobbing machine offers high rigidity, reactivity and precision.
«The high stiffness – Matteo Tonelli comments – is achieved thanks to the use of preloaded recirculating roller guides and of special locking of the shifting carriage, with high-load backlash-free deformation, positioned under the hobbing axis. The reactivity and gain of the axis of the hobbing rotation are obtained thanks to the use of a high torque motor integral to the spindle, equipped with an absolute Heidenhain ring encoder directly keyed on the same to maximize the accuracy .Finally, the heat stabilization, essential to ensure the process repeatability , derives from the recycling of refrigerant oil purposely studied inside the structure and from automatic compensation system that acts through thermal probes».
The machine can receive pieces with maximum diameter of 500 mm, nominal module 8-10 with a maximum hobbing width of 600 mm.
«A capacity – Mr. Tonelli points out – that allows machining a wide range of shapes, including shafts , by offering in this way flexibility also to subcontractors performing frequent changeover .At the same time, it is also suitable for manufacturers of mass-production , thanks to the possibility, for instance, of inserting the optional two-positions ring loader system equipped with an anti-collision device, for fast loading».
The added-value of the digital twin in production
The machine integrates the Cnc numerical Sinumerik One control system, the latest technological frontier of Siemens, which enriches the new EVO 400 CNC with interesting features, such as the creation of a digital twin to improve corporate efficiency and to optimize industrial processes. Moreover, it consents the simulation of piece programming and machining operation, ensuring a preventive collision control.
«The user-friendly retooling – Tonelli adds – is also assured by the Cnc Sinumerik One, with an interface that has been fully customized and simplified to make it intuitive».
Comur, in line with its corporate policy, includes in the machine both standard machining software and special part programs, in-house developed, without additional costs.
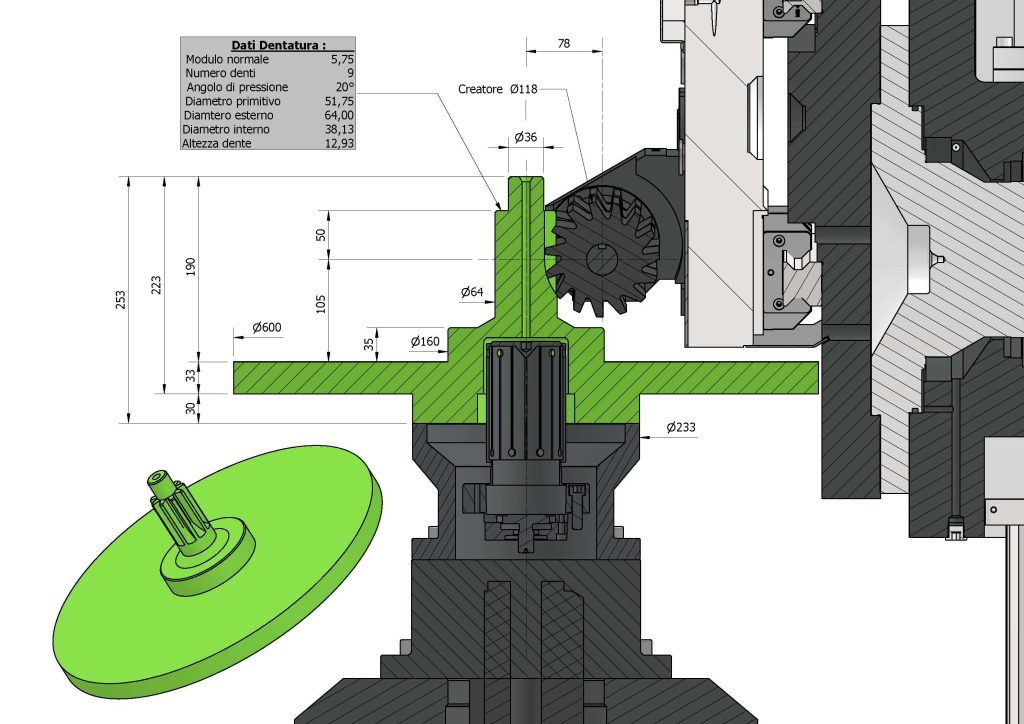
The manufacturing future, in small and big
The new EVO 400 CNC represents for the company the standardization of a new range soon, joined by other models.
«The next machine – Mr. Tonelli confirms and concludes – will be constructed on the same structure as EVO 400, with modifications made to the hobbing head and to the worktable , which will have a smaller size , it will be more streamlined, faster and more dynamic. It will therefore be a smaller size, a 200 model.
The next step will be instead the implementation of a gear shaping machine, exploiting the base structure of EVO 400 already studied for this purpose. Compared to our already known gear shaping machines, the new machine will have a plus in terms of technology and features. In fact, it will be equipped with Z axis, with adjustment of the hobbing stroke by CN, and it will also be equipped with electronic guide, which will allow generating both straight and helical toothings, without needing any mechanical set-up».