Established in the early Eighties as commercial company, in 1984, due to a strategic merging, the Italian company Faro starts the production of special bearings but precisely in 1989 the expansion begins, with the management of new members and the rise of capital.
In the following years, the new managers’ philosophy has always been reinvesting profits in new production machines, control equipment and, mainly in human resources. The pressing market demands, combined with a further strategic integration with an enterprise highly skilled in the technology of manufacturing processes, allow Faro to double the turnover, starting a total upgrading programme of the machine fleet with the introduction of increasingly cutting-edge equipment.
In 1997, the inauguration and the move to the new factory constituted the preliminary assumption to increase even more the production capacity and a more and more efficient customer service.
Aware of environmental problems, the company is concretely committed to minimizing the environmental impact of processes, products and services and to certifying the reliability of the environmental management system so applied, achieving the ISO 14001 certification in 2005 and afterwards obtaining also the certification of the ISO 9001 Quality Management System.
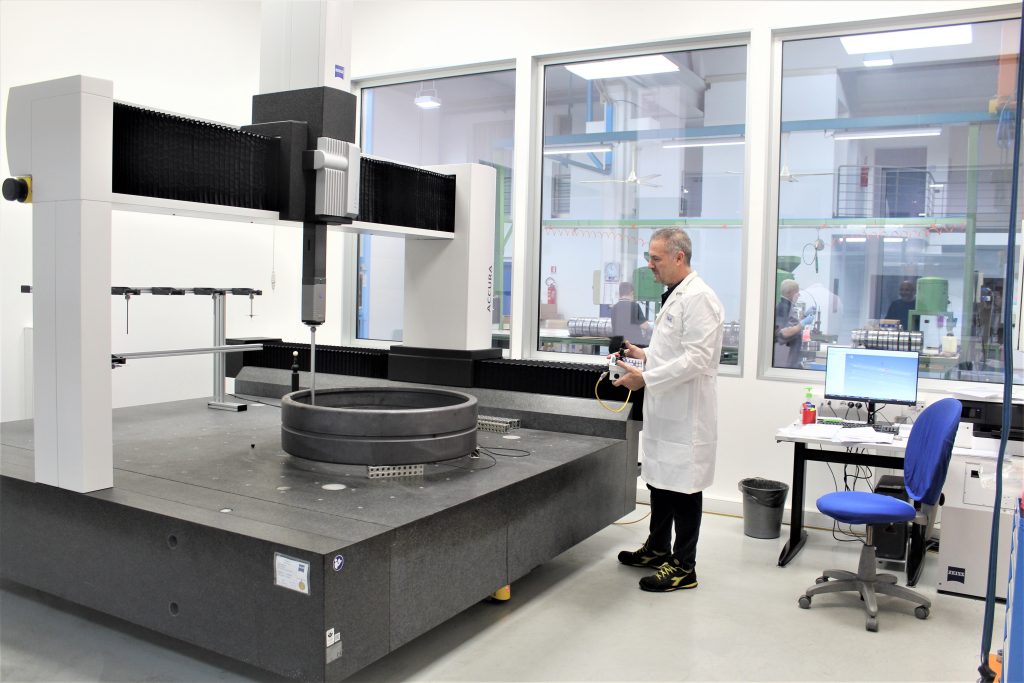
The quality control is the feather in the cap
Speaking of special production, often manufactured also in small batches, the quality control is fundamental.
Along the years, the company has been equipped with a Quality Control chamber that includes, besides state-of-the-art tools (with as many as 1,200 present measuring instruments), a machine that can check and calibrate all measuring equipment installed.
Having to execute measurements in the order of microns, the precision and the perfect calibration of all systems is an issue that cannot be given up.
With over 40 years of expertise, Piacenza company is highly specialized in the design and manufacturing of radial and axial bearings and, due to a highly skilled staff and a cutting-edge machine fleet, it promptly meets the requirements of various sectors, among which iron and steel industry, handling, Oil&Gas, machine tools, power transmissions, paper converting and the delicate sector of wire/rope making machines, offering a product with excellent qualitative standard and particularly competitive deliveries.
Moreover, pursuing a constant improvement, in 2019 Faro has made a huge investment, building, inside its factory at Calendasco (PC), a new metrological laboratory that takes up 100 sq.m. and consists of two class-1 temperature-controlled chambers (20° with admitted variability of 0.5°C/hour, 0.5°C/day and 0.5°C/metre), separated by a settling-in chamber.
The laboratory hosts two Zeiss three-dimensional measuring machines that, with different characteristics, have allowed increasing the dimensional control performances and perfecting the shape control, reaching a diameter of 2,000 mm.
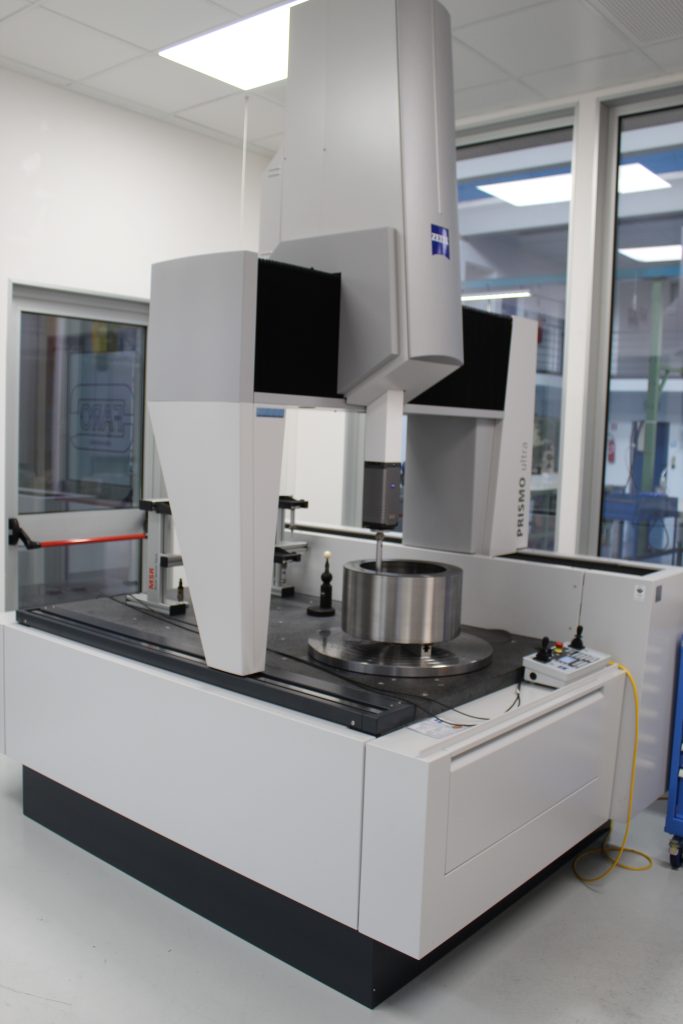
Zeiss Prismo Ultra 3D is a bridge measuring machine made of composite materials of carbon fibre and ceramic. The equipment uses corrections guided by computer of all dynamic influences on the machine, so optimizing the precision during the high-speed scanning. The precision obtained in measurements is in the order of a tenth of micron. Equipped with a rotary integrated RT-AB table resting on air bearings, it combines a perfect motion with a very accurate detection of shape values and it extends the control possibility up to a diameter of 1,000 mm. Besides being a conventional three-dimensional control machine, Zeiss Prismo Ultra 3D is equipped with a geometrical control system and performs the roundness meter function for notable sizes and weights.
Zeiss machine, Accura model, in bridge configuration too, is made of steel and aluminium with a control range extended to the maximum sizes of 2,000 x 2,400 x 1,000 mm, with an active fixed measuring head of high precision and stability. With this cutting-edge machine, equipped with advanced systems, Faro has hit the target of fully satisfying the requirements of its production, in a sector where precision and quality are more and more important.