Atlas Copco Industrial Air is launching GA 11-30 FLX, which is their first dual-speed compressor. Thanks to the dual-speed technology, the start-up peak, unload power and transient losses are significantly lower than the ones in their other fixed-speed compressors. This means that up to 20% less energy is needed compared to Atlas Copco Industrial Air’s traditional fixed-speed compressors, making the GA FLX their most energy efficient fixed-speed product. The compactness of the product and the fact that the GA 11-30 FLX can deliver optimal flow at all different pressures and not just a specific pressure variant, is what makes this product so unique.
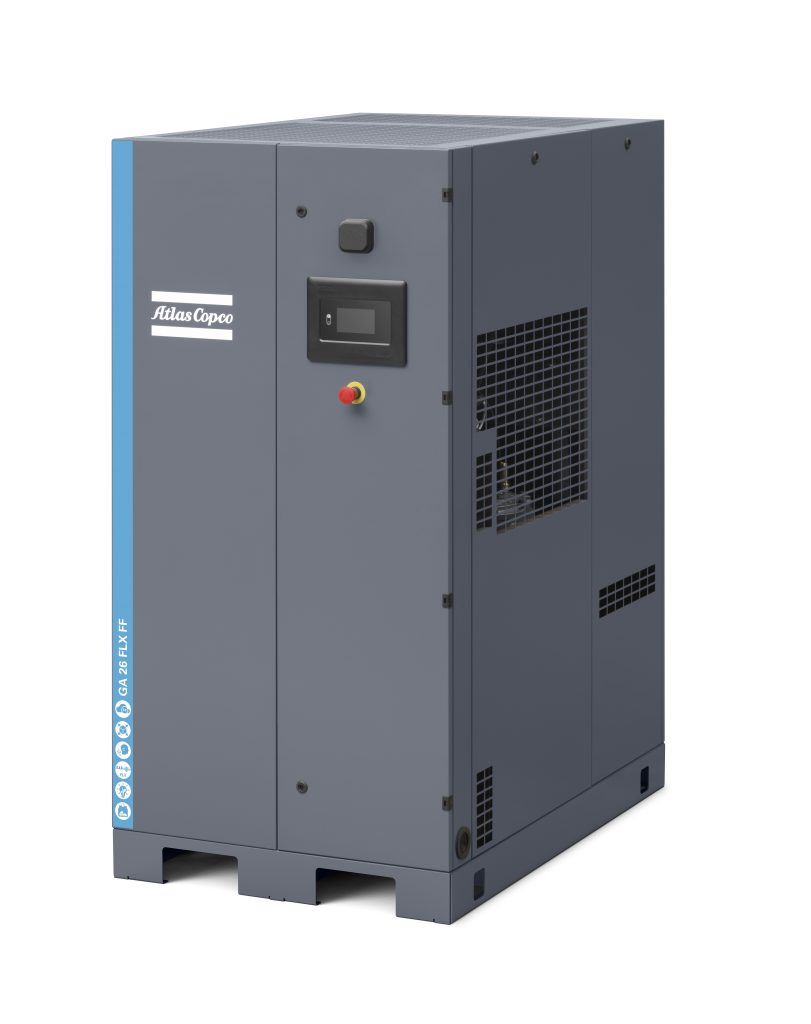
Market demand creates sustainable innovation and flexibility
The idea of GA 11-30 FLX originated from the increasing market demand for more energy-efficient products. Considering the energy crisis during the winter of 2022, the market is now more than ever aware of the financial benefits of a more sustainable product, saving energy and therefore extra costs.
Atlas Copco Industrial Air’s newest compressor, GA 11-30 FLX, has a significant impact on clients’ energy usage and the environment. With its dual speed drive train and motor, the start-up peak, unload power and transient losses are significantly lower than the ones in their traditional fixed-speed compressors.
More specifically, this means that up to 20% less energy is needed compared to Atlas Copco Industrial Air’s traditional fixed-speed compressors. Seeing as worldwide 5% of energy is used up by compressors, this product reduces its global impact.
On top of that, its actual footprint is also an innovative feature in Atlas Copco Industrial Air’s fixed-speed compressor category. The drive train set of this compressor can be placed vertically, making the footprint of the compressor much more compact and thus saving a lot of space.
Joeri Ooms, Divisional President Atlas Copco Industrial Air: “At Atlas Copco Industrial Air, we work towards a more sustainable world every day. We are the cradle where tomorrow’s innovative industrial ideas are shaped, with focus on environment and people. GA 11-30 FLX is our best fixed-speed compressor and is our answer to client’s demands for more energy efficiency.”
Atlas Copco Industrial Air’s experience shows that the market does not only have a need for more energy efficient products, but also more flexible ones. Thanks to the GA 11-30 FLX, customers are not limited by the maximum working pressure of the compressor. The GA 11-30 FLX uses its power optimally to deliver as much air as possible at all set pressures, thus using the energy more efficiently and consequentially operating more sustainably.
Other fixed-speed machines only deliver optimal flow for their own pressure variant. As a result, higher pressure variants of their traditional fixed-speed compressors deliver less air at lower pressures and lower pressure variants cannot operate at higher pressures. The fact that GA 11-30 FLX can deliver optimal flow at all different pressures is what makes it so unique.
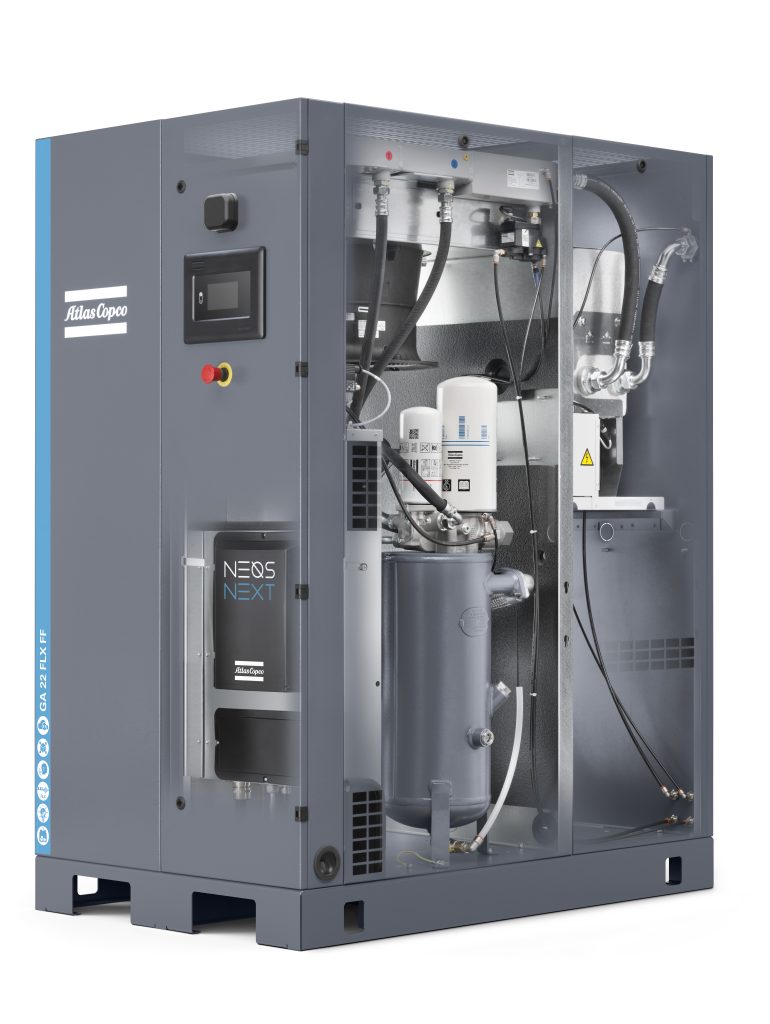
In-house design with proven technology
This product is a result of building on years of experience and proven technology that works and is reliable. The compressor is produced in Montecchio, Italy and in Antwerp, Belgium, where the Atlas Copco Industrial Air production teams are practicing lean manufacturing. In other words, they can optimally follow the demand seeing as they can alter the production process quickly if need be. Training, attention to details and multiple tests are central during the production process to guarantee the best possible quality.
Joeri Ooms: “Our customers’ insights were taken into account in every step of the development of the compressor, thanks to the involvement of our local sales offices, also known as our customer centers. We are very proud of the in-house design of all the principal components of this product, which is a result of efficient collaboration between all the Atlas Copco cross functional teams and colleagues globally.”
After a year, customers are given the opportunity to upgrade this fixed speed compressor software-wise to VSD (Variable Speed Drive) technology. The built-in controller analyzes the data during the first 1.000 hours of operation of the machine, and shows how much additional energy a customer could potentially save on top of the previously mentioned 20%, if they were to upgrade to VSD technology. The controller will express energy savings in kW/year. Based on this calculation, the customer can decide if the upgrade to VSD is worthwhile for their case.
More information on the product can be found here.