Atam invested in six new overmoulding presses for increased productivity, flexibility and total control of the encapsulated coil overmoulding process
ATAM has recently completed the replacement of the majority of its overmoulding presses at the Agrate Brianza plant, adding six new machines, each one with a different tonnage. This major investment allows the company to improve production capacity, flexibility in switching from production of one encapsulated coils to another, and it offers the possibility of having total control of overmoulding, namely one of most critical phases of the entire production process.
The six new overmoulding presses have each a different tonnage in order to be used in a diversified manner. The biggest will be used to produce large coils, while the other five, each with lower tonnages, will be used for moulding the remaining coil sizes.
The six new ERGON overmoulding presses are one-offs and are built from a basic structure shared with the manufacturer, DM Industrial Srl – TURRA Division, that has a long-standing partnership with the company, and are the result of a specific customisation requested by ATAM, which contributed its expertise in the production of encapsulated coils and machinery management software.
The co-design project concerned first of all the layout, which is now more compact, and then focused on a series of technical details to achieve set objectives, such as higher productivity, flexibility and total process control, all taking into account the operator’s ergonomics and safety as guidelines.
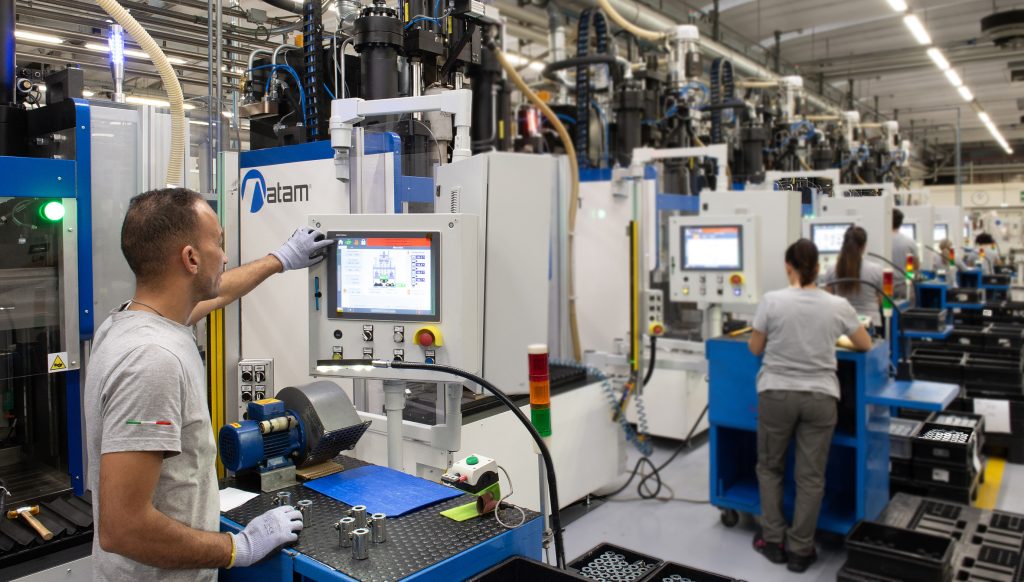
The requested customisations have for example led to the positioning of two monitors on the machine positioned in such a way that the operator can constantly have visual control of the machine parameters, and therefore the progress of the production process, on one monitor and the parameters controlling the product, its technical design and warning signals, on the other, all in real time. Other customisations that characterise the project have also made it possible to optimise the operator’s cycle time and bring it as close as possible to that of the machine, all to the benefit of productivity.
Another technical measure, which involved an automatic mould loading system, increases the processing speed and consequently reduces the time to market, a valuable aspect for clients in times of uncertainty characterised by fluctuating demand with peaks and stagnation. A further benefit is the flexibility to switch from the production of one type of encapsulated coil to another. This feature is particularly important for production lines, such as ATAM’s, which are highly customised and geared towards medium-low volumes.
The customisation of the presses also involved their integration with the internal process methods, control parameters and data analysis procedures, thus improving the overall control of the process. The machine itself monitors the process, automatically keeps all set parameters under control, and, by communicating with our ERP System, is able to send compliance feedback during the process itself.
The capacity to read the main parameters during the production process leads to a quality control system directly on the machine, to which an indirect control is added. All the collected machine parameters are extrapolated and analysed offline by ATAM’s internal system. The customisation required by ATAM concerns above all specific parameters, which in some cases exceed the standards, considered essential by ATAM for ensuring first-class product quality. This type of analysis benefits greatly from the machine’s innovative sensing and real-time feedback on product quality during the process, which is only possible using the new instrumentation.
ATAM is thus able to offer product quality control already during production and no longer as in the past in post-production with final tests, thus reducing both scraps and failure rates.
The possibility to make substantial investments in the constant modernisation and upgrading of its industrial equipment makes ATAM a benchmark company for the design and production of encapsulated coils and industrial connectors for pneumatics, hydraulics and process valve applications.