Set up in 1952, Rastelli Raccordi is managed by the same family still today. In time, due to the creation of an efficient organizational structure and to the constant adoption of new technologies, the company headquartered at Villanterio (Pavia, Italy) has widened its offer range, establishing itself as a market leader in Italy and as one of the primary players on a European and global scale. To date, Rastelli faces market challenges going on innovating with advanced technologies, in both manufacturing processes and in products themselves, in order to grant higher quality and added-value for customers. Barbara Rastelli, Chief Executive Officer, illustrates us the main novelties that are characterizing the company in these months.
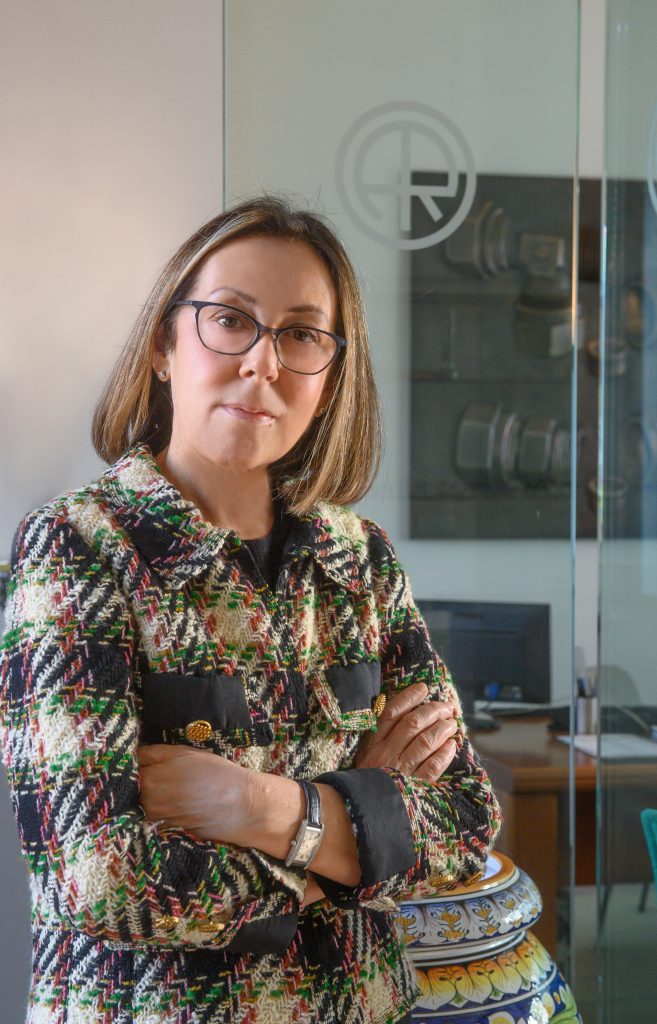
What is the added-value that today is acknowledged to a historical company like yours?
Whenever a hydraulic plant is assembled, we need the availability of simple, but at the same time sophisticated, components, fittings. The latter have strongly evolved in time and today they represent an important element, which must necessarily provide certain performances and reliability in time. Our company has always structured its policy by investing in fundamental factors like research and development, keeping the focus high on quality and environment protection and trying mirroring at best customers’ requirements, also in terms of costs. Today we are acknowledged as one of the historical fitting manufacturers operating in the global market, also due to the quality/price ratio that makes particularly appealing our product made of galvanized steel and stainless steel, subdivided into three primary ranges, with cutting ring DIN 2353-24°, for flared tubes SAE J 514-JIC 37° and hose couplings. Moreover, as range completion, it is worth mentioning BSP-BSPT-NPT adaptors, too.
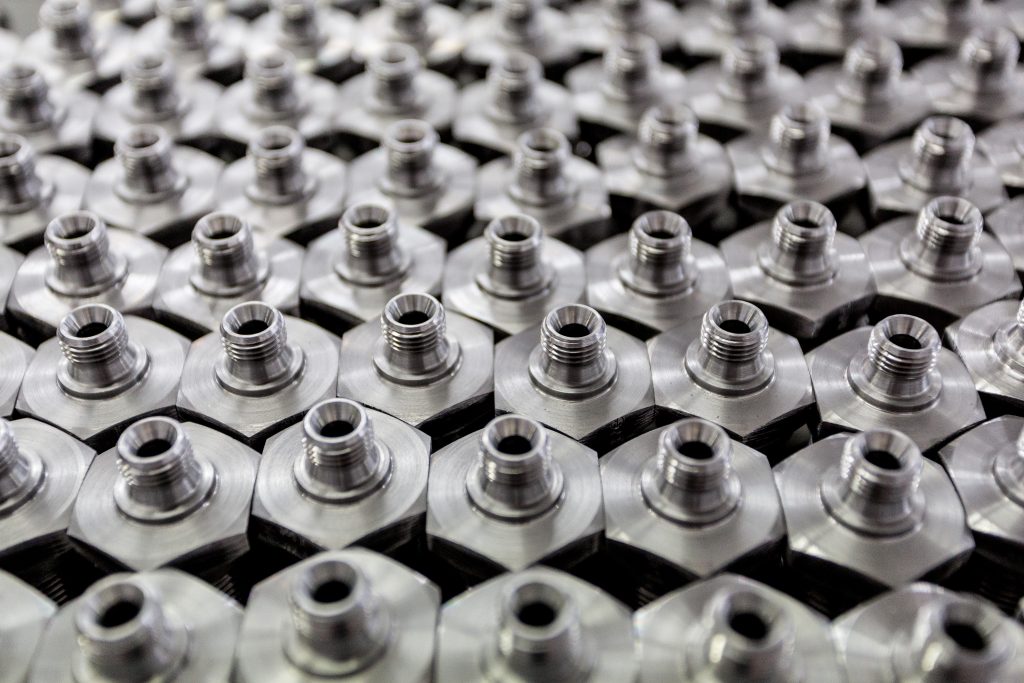
The corporate range includes carbon- and stainless-steel fittings, fittings for flared tubes and hose couplings, 60° adaptors, gas series fittings, non-return valves, ball valves and brackets
How is the unceasing innovation concept declined?
2023 was a particularly important year for us precisely from this point of view, to the extent we can say we have generated a turning point for a more efficient and efficacious operativity. To make this happen, it was decisive the introduction of a new managerial system, which has allowed us to undertake the definitive solution in the company’s all operational phases, from design to shipment, making the system perfectly compatible with the highest corporate standards demanded by an increasingly exacting and competitive market. Moreover, we can add that last year, in March, the hard work undertaken allowed obtaining also the UNI EN ISO 14001:2015 certification, of which we are particularly proud because it awards our efforts also in the issue of the attention to environmental sustainability policies.
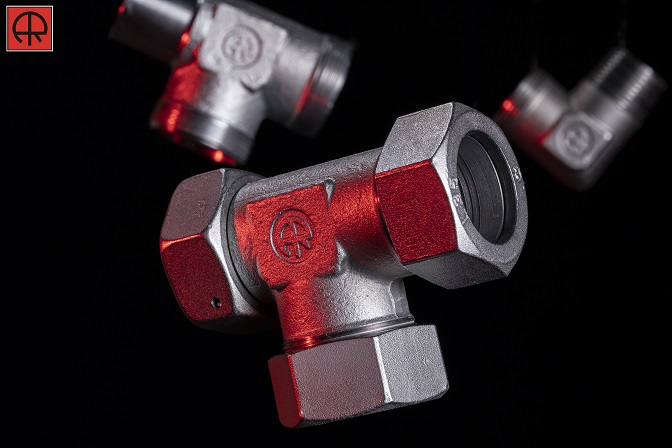
What novelties, instead, from the manufacturing point of view?
In production terms, we have accomplished and made the new galvanizing department operational, implementing it in strict collaboration with our engineering team, who has permitted us to achieve the new protective Zi-Ni TOTAL SCREEN (RRTS) coating included in the REACH regulation. This new exclusive treatment, about which we might deeply debate, essentially occurs in absence of hexavalent chrome and cobalt and therefore it is perfectly compliant with the European UE2000/53/CE/RoHS standards dated 2007. Moreover, the high penetration capacity of the bath assures the electroplating in each spot of the fitting, even in the least accessible areas, that is to say the inner ones, which in moulded shapes are always hardly accessible. The improved and homogeneous protective layer coating of Nickel (12-15%), obtained inside a broad range of current density, then assures a high stability of the result in time. The successive phases consisting of passivation and sealing have allowed reaching much higher technical performances and resistance to the red plague corrosion than the normal standards commonly on trade. Test results have given really exceptional outcomes.
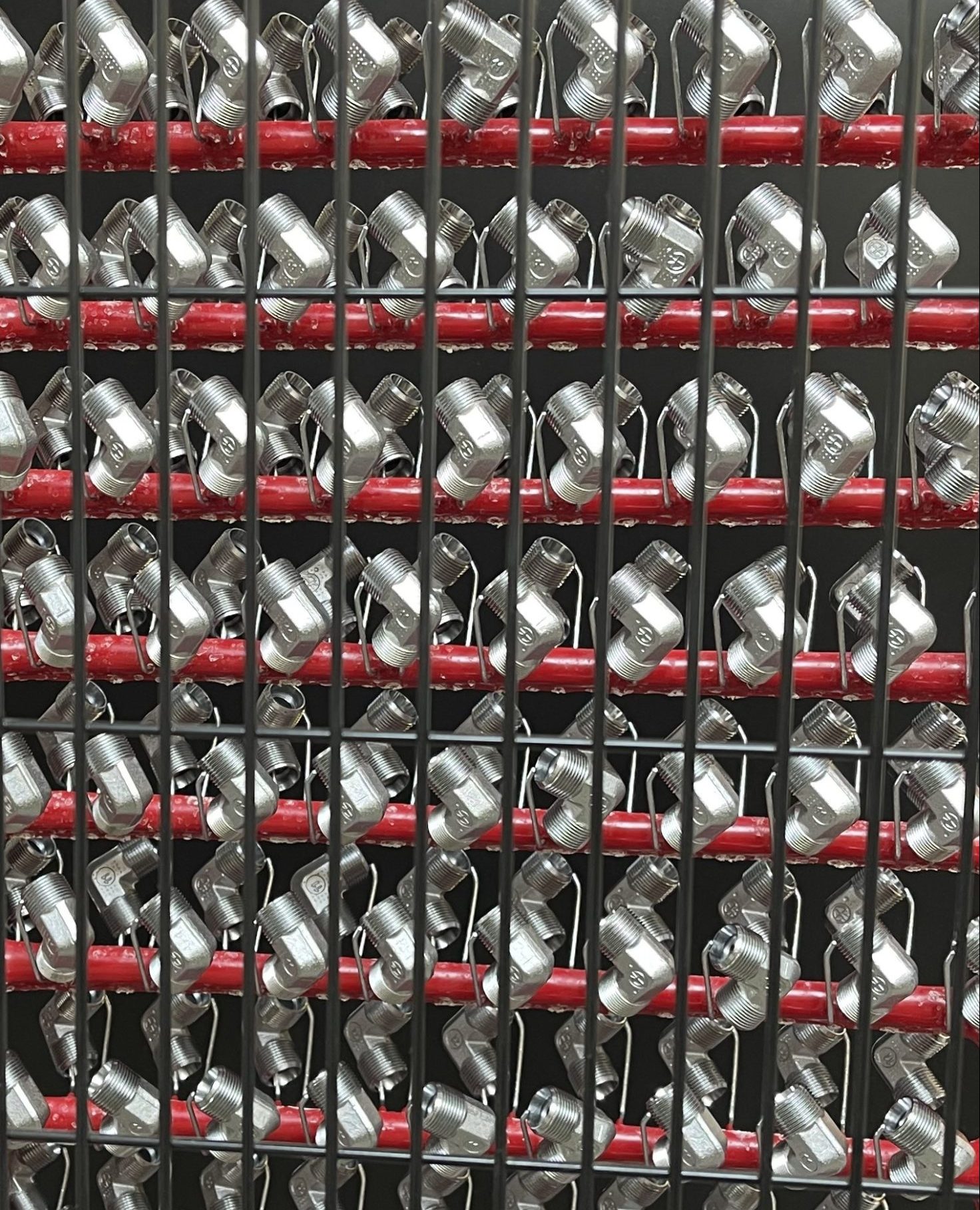
Furthermore, this year we have started a new phase of our production, introducing and starting the manufacturing renovation according to industry 4.0 machines. The first transfer machine of this project, fully developed in collaboration with our design team, is today operational. We are very satisfied with the result obtained, having activated the control and the full management from remote, exponentially increasing the productivity that exceeds previous ones by over 30%.
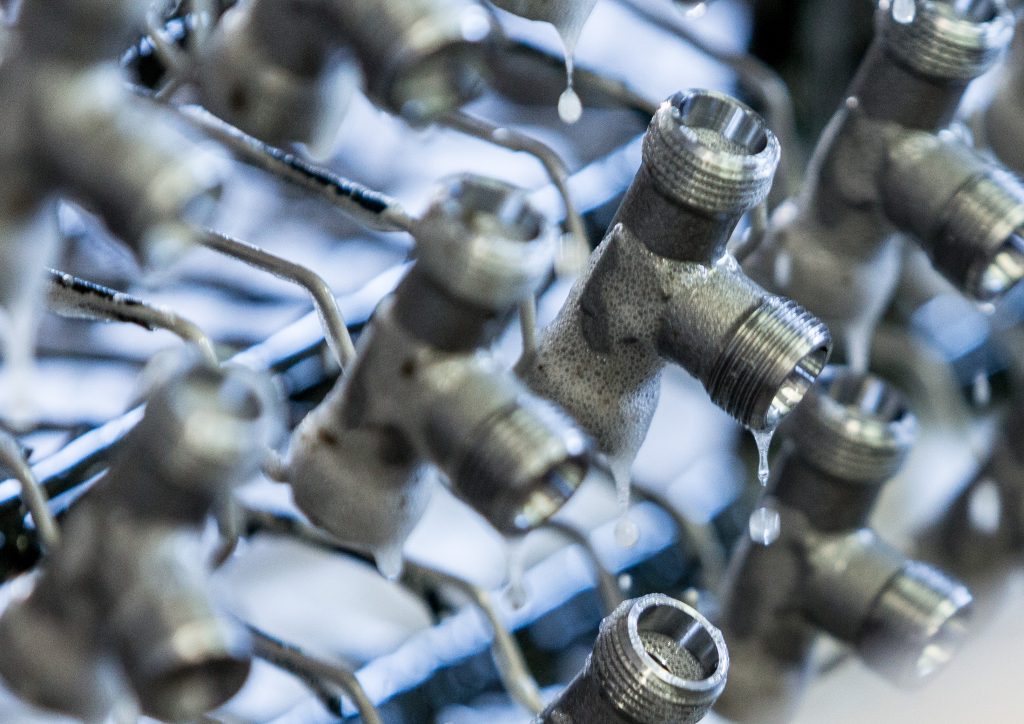
What solutions have you implemented to improve the service quality?
Essentially, adopting in time solutions that have allowed the complete automation of the provisioning and packaging chain and of all those operations that lead to shipment, following the goods-to-man principle.
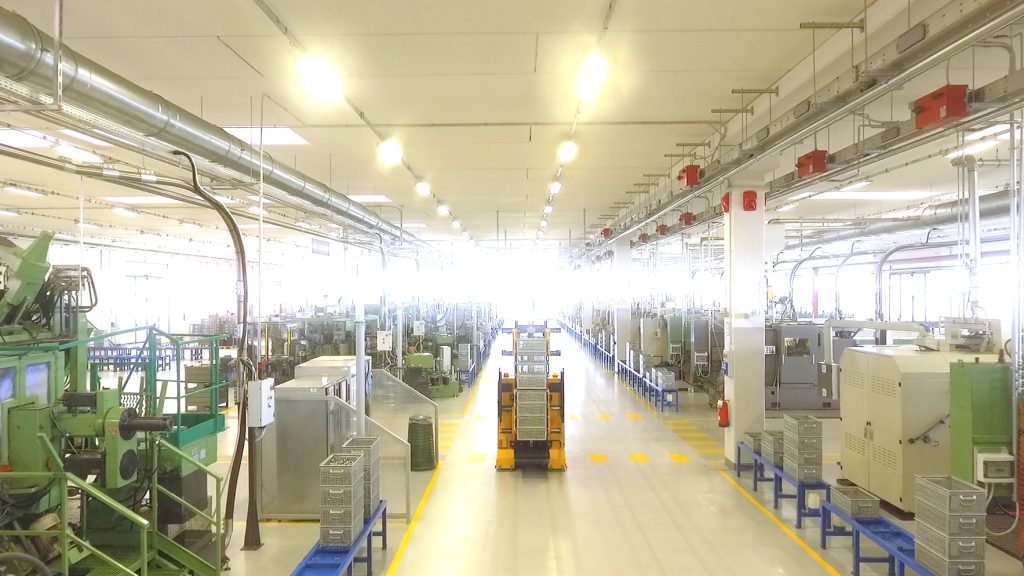
The whole of these solutions has permitted to increase precision and efficacy, shortening the average delivery time to customers by 25% and, at the same time, to improve operators’ ergonomics and safety standards. Today our warehouse, which includes a hive of 17,000 cells with a handling of about 1,000 cells a day through two stacker cranes that operate in random modality, can manage 29000 codes and handle 50 million pieces every year on average.
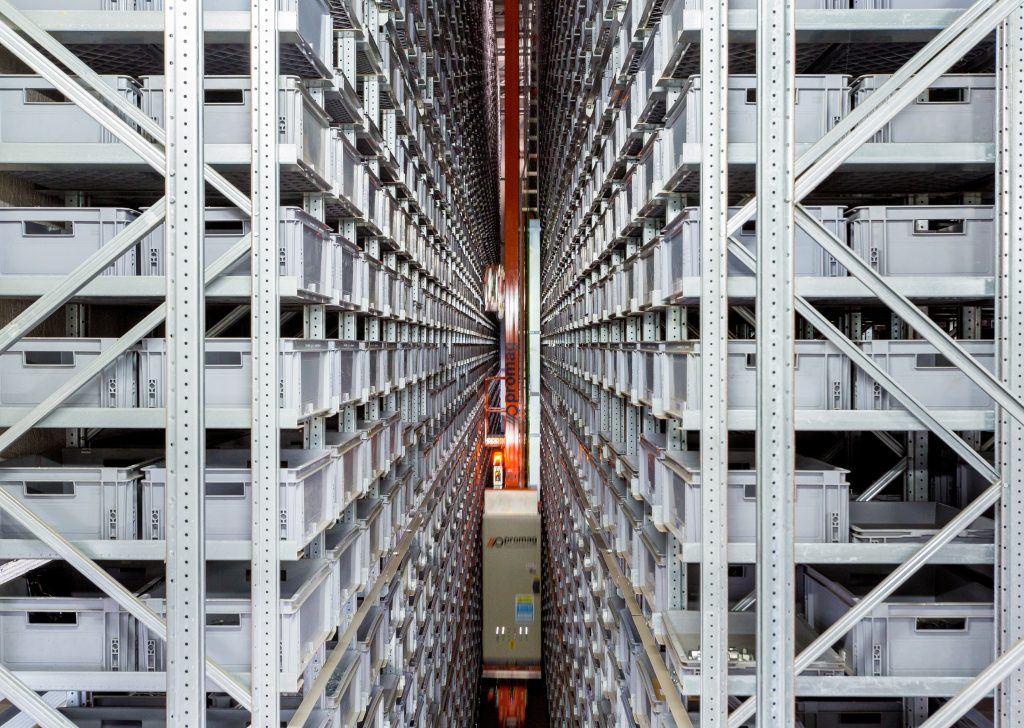
The fully automatic system allows the shipment customization, up to the simultaneous fulfilment of different job orders for the same customer, in separate packages if demanded, and for different destinations and customers. Moreover, it also allows the combination with kanban management systems, with which distributors are increasingly called to deal. Still referring to machining quality and integrity, the storage is made in boxes with pieces suitably positioned for preventing their collision and where necessary with shaped separators, so avoiding eventual damages on threads or on machined parts.