Atlas Copco proposes cutting-edge products and solutions to reuse heat generated from air compressors
A responsible use of available energy sources in production processes is essential to guarantee the environmental sustainability of industries. With this in mind Atlas Copco has developed new products to recover heat generated from air compressors: the objective is reducing, and eventually completely eliminating, the use of methane boilers for the production of hot water used in industrial processes. This regards the use of the heat generated by air compressors, usually dissipated into the environment and therefore wasted, to heat the water used in industrial processes. These are interventions that fall within the decarbonisation objectives indicated by the PNIEC (National Integrated Plan for Energy and Climate) which, as regards Italy, set an indicative target of reducing consumption by 2030 equal to 43% of primary energy, corresponding to an annual decrease in final energy consumption of 9.3 Mtoe.
Energy conversion helps reducing greenhouse gas emissions, improving energy efficiency and reducing operating costs in sectors that use a lot of heat and energy, such as the food and pharmaceutical industries. To do this it is necessary to analyse processes, identify needs, classify energy consumption, then find technologies and solutions to reduce the carbon footprint and obtain maximum energy savings.
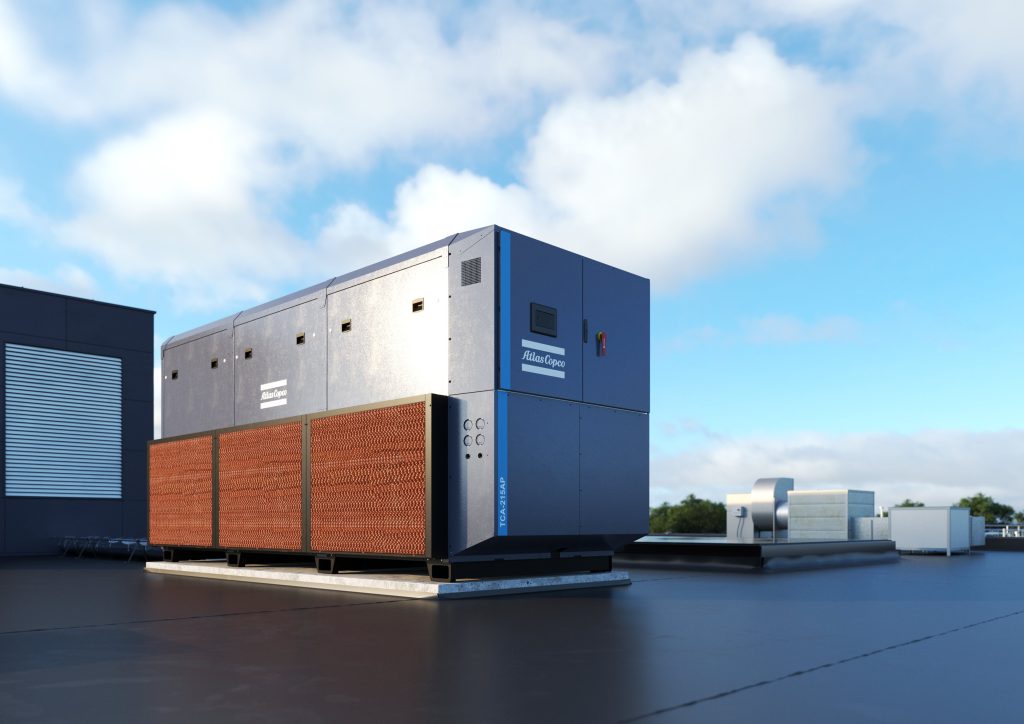
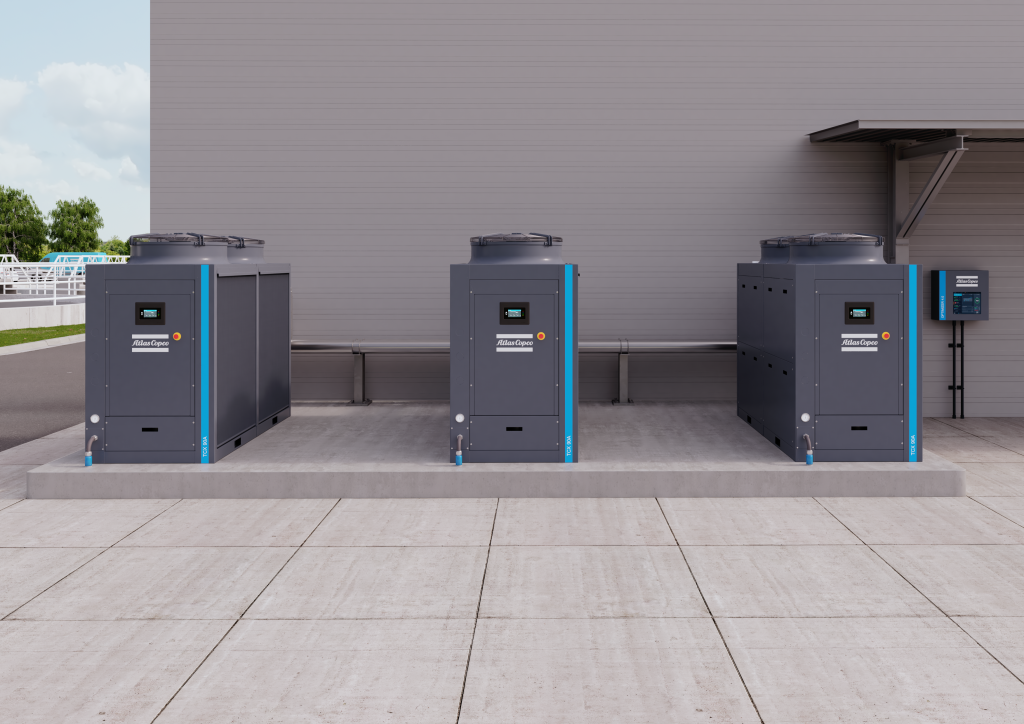
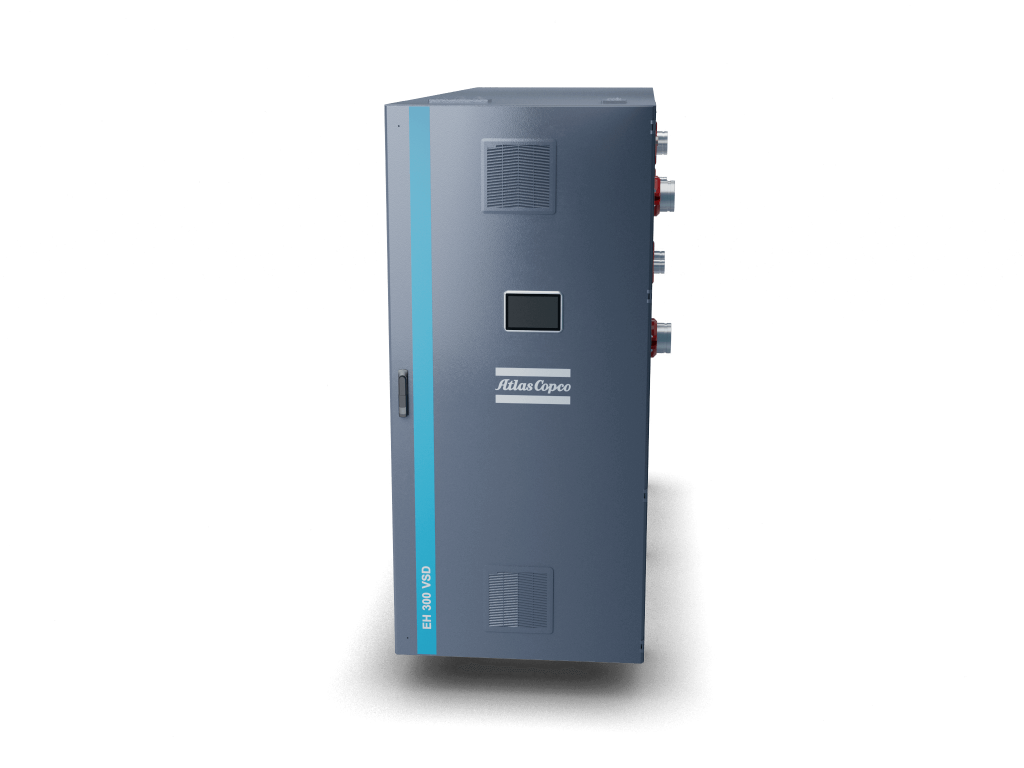
The offer for energy conversion defined by Atlas Copco includes different types of products, to be used according to customer needs:
- energy recovery system, a device that captures the waste heat from the compressor and transfers it. It can recover up to 94% of the electrical input power as heat and allow hot to obtain hot water up to 90°, used, for example, for district heating and/or domestic hot water.
- industrial heat pumps, which transfer heat from a low temperature source to a system requiring high temperature, using a refrigerant as an intermediate working fluid. In cases where they use waste heat from the compressed air system as an input, they help reducing energy consumption and carbon emissions.
- systems for cooling process water, essential in production processes, where processes must be maintained at a low and constant temperature.
- steam compressors, the last frontier of energy conversion
An interesting project
At this regard it is interesting to mention the project carried out by FrieslandCampina Ingredients, an established multinational of Dutch origin that operates in the protein and prebiotics sector. This is an energy conversion system, created in cooperation with Atlas Copco, which reduces by more than 60% the energy required for the spray drying process used for the production of powdered dietary ingredients. The project involves sending the waste heat generated during the spray drying processes to a heat exchanger, then to a water heat pump that produces low pressure steam. The same steam is compressed until it reaches a temperature of 190°C and then used to heat the air necessary for the atomizer.
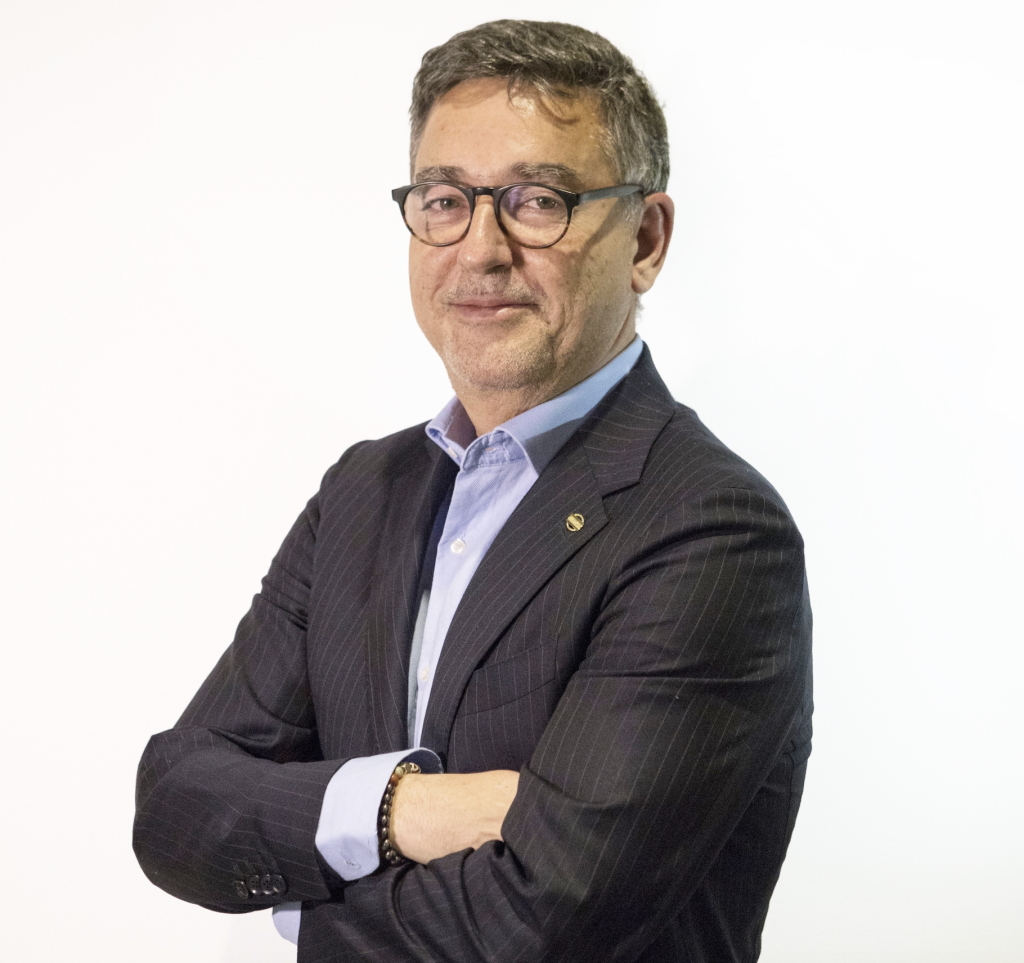
«Energy conversion represents a strategic extension of our offer: our objective is in fact to contribute significantly to the sustainability of the industry in the future, capitalizing on the experience gained over years of research and development on the energy efficiency of compressors. In Italy we are cooperating with several customers to explore the potential of energy conversion. We found a lot of interest, showing that the Italian industry is highly oriented towards environmental sustainability», states Juan Manuel Tejera, General Manager of Atlas Copco Italia – Compressors Division.