In recent years, advancements in robotics including collaborative robots and exoskeletons are enhancing human capabilities and contributing to automating hazardous tasks. However, one challenge remains: actuators, the components responsible for robotic movement, are bulky and energy-intensive, limiting the large potential of these devices.
Modern robots, especially humanoids, need lightweight yet powerful actuators to move like humans. Human joints generate impressive torque at moderate speeds. Achieving similar movement with machines demands lightweight actuators capable of producing very high torques. Currently, this is done combining electric motors with high-ratio gearboxes, but the resulting actuators are still significantly heavier and bulkier than human joints.
Off-road machines, such as excavators, require also high torques at moderate speeds and actually share a lot of similarities with human movement. In off-road machinery, hydraulic systems are used to achieve these high torques with relatively low weights. Their actuators have inspired robotic engineers to explore the use of hydraulic actuators in robotics. A well know example is that of Boston Dynamics’ ATLAS, which originally used hydraulic systems and reached impressive movement performance. However, modern robotics is decidedly converging towards electric motors and high-ratio gearboxes, and even Boston Dynamics’ newer ATLAS has now electric actuators, as do other leading humanoid robots like Tesla’s OPTIMUS, or Figure’s 01.
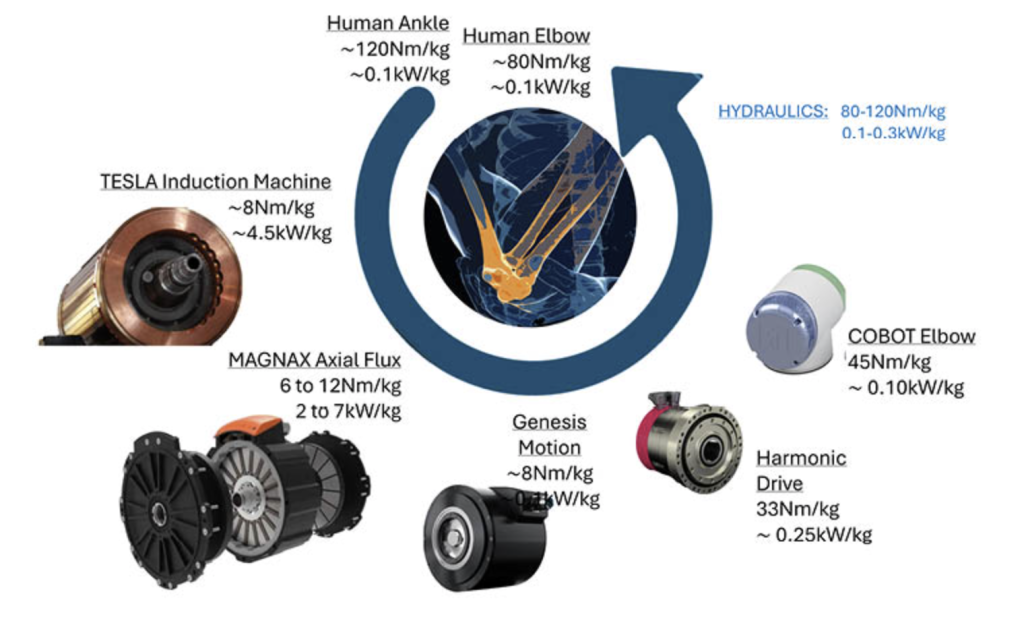
While electric motors are more efficient, they require gearboxes to compensate for their limited torque density. High-ratio gearboxes (typically over 100:1) are essential in robotics, allowing small motors to generate the necessary torque by trading it for speed. Strain-wave gearboxes are dominant due to their precision, but other gearbox technologies, such as cycloidal and planetary systems, offer promising alternatives, especially in industrial and heavy-duty applications.
The recent electrification trend of off-road machinery mirrors the challenges faced by robotics. Heavy-duty machinery like excavators demands high torque densities, efficient power management, and durability. The off-road sector is investing heavily in transitioning from hydraulic systems to electric motors combined with high-ratio gearboxes. Though smaller machines are already using electric power, larger machinery still relies on combustion engines and hydraulics due to the huge torque requirements.
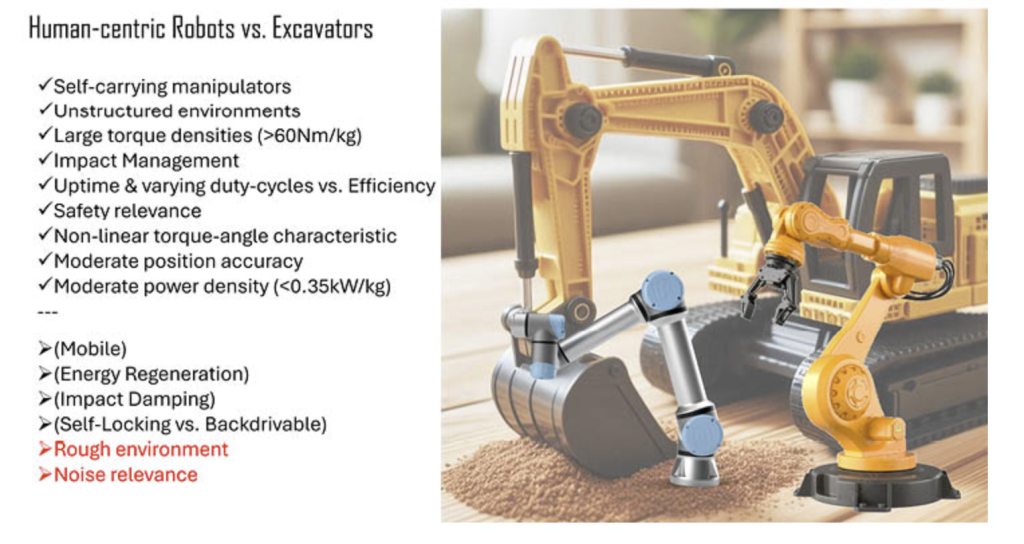
Gearboxes will also play a pivotal role in this electrification journey. Advanced gearbox technologies, paired with high-voltage electric motors, could meet the torque and power demands of off-road machinery. Dual-motor actuation, inspired by hybrid vehicles, offers a versatile solution to handle variable operating conditions with electric actuators. Energy recuperation, enabled by optimized backdrivable gearboxes, will further reduce battery size and enhance efficiency.
Conclusions
In conclusion, gearboxes are at the core of modern robotics and the future electrification of off-road machinery. By addressing the challenges of torque density and energy efficiency, gearbox innovations will drive the shift towards sustainable and high-performing heavy-duty machinery.
References
- Geimer, Marcus, and Christian Kunze, „Hybride und energieeffiziente Antriebe für mobile Arbeitsmaschinen“, 9. Fachtagung, Karlsruhe, KIT Scientific Publishing (2023): 106.
- Danzer, C., Poppitz, A., Pirkl, T. et al. „Elektrisches Antriebskonzept mit Standardkomponenten für schwere Nutzfahrzeuge.“ ATZ Heavy Duty 14, (2021): 10-15.
- García, Pablo López, et al. “Compact gearboxes for modern robotics: A review.” Frontiers in Robotics and AI 7 (2020): 103.
- Verstraten, Tom, et al. “Kinematically redundant actuators, a solution for conflicting torque–speed requirements.” The International Journal of Robotics Research 38.5 (2019): 612-629.