The attention to the environmental pollution and the rise of business costs caused by energy prices is driving markets to the research of solutions and technologies that allow efficiency and saving.
The most efficient way to generate hydraulic power: the Smart SSP servo-pump
The answer by Atos Group comes with a range of suitable products for intercepting these requirements, like the series of energy-saving servopumps with p/Q control, which permit to optimize the energy use, up to even 80% less than a conventional system. In comparison with products commonly diffused on the market, the Smart SSP servo-pump delivers only the necessary quantity of hydraulic power to satisfy the work stage to be carried out, surpassing the systems based on synchronous motor that rotates at constant speed to generate pressurized oil even when not required during the working cycle of the machine. The results of the comparative tests carried out on a 300-ton plastic injection moulding machine, for instance, show that the energy consumption of the servo-pump is 80% lower than fixed-displacement systems, leading to a saving of 75 MV and of 11.7 tons of carbon dioxide.

Accurate research
Fruit of an accurate work of the R&D Department of the company headquartered at Sesto Calende (Varese. Italy), the Smart SSP servopump is provided with various innovative functions that make it efficient and user-friendly. Among them, the Smart Start-up function, which notably simplifies the startup of the servo-pump through a fast and intuitive guided procedure, which includes the configuration, the control of the electric motor tuning and the autotuning of the servopump, enabling the best possible dynamic response with just three steps. Besides, the electro-hydraulic skills gained in Atos have permitted the development of a specific control algorithm (p/Q), purposely designed for the hydraulic axes. Thanks to it, the manufacturers of hydraulic machines will no longer need to develop their own control algorithms.
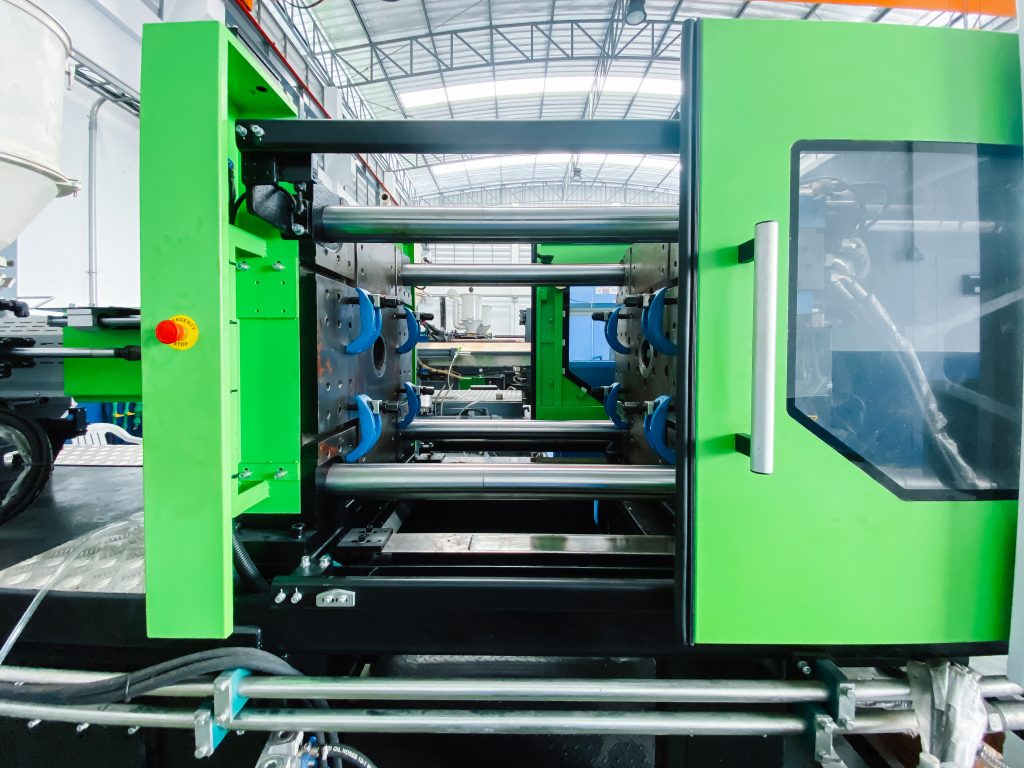
Patented algorithms
The autotuning function was born from numerical simulations and from the tests of the research and development sector, which have been the key to develop various patented algorithms that simplify the commissioning and the management processes of SSP servopumps. With the autotuning function, proceeding to manual setups is not necessary, since the process of servopump parametrization is automatically carried out, to obtain the best dynamic response, granting precision and stability during pressure control phases. To prevent temperature peaks during the prolonged phases of pressure control the Smart Cooling function comes into play and, through an algorithm, it can estimate the inner pump temperature without using transducers. If a surpass of limits was detected, a drain valve would come into action and permit an oil recirculation, thus obtaining the temperature decrease in the pump. This function enables an extension of the system service life. The SSP control algorithm also allows the real-time selection of the optimal configuration of the cylinder to be checked, for the best performances of each single machine motion.
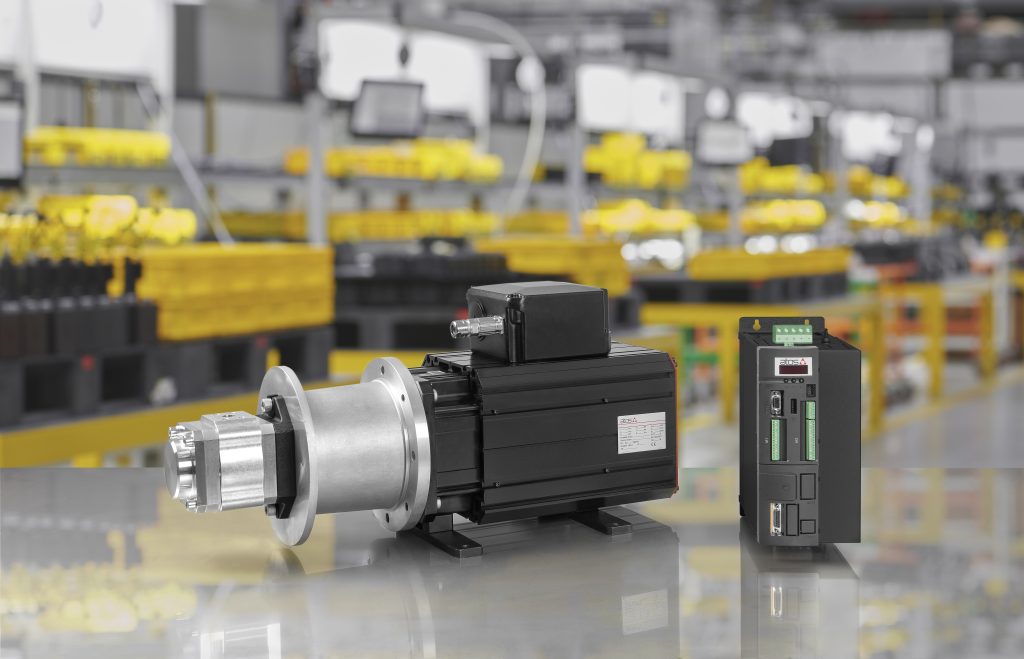
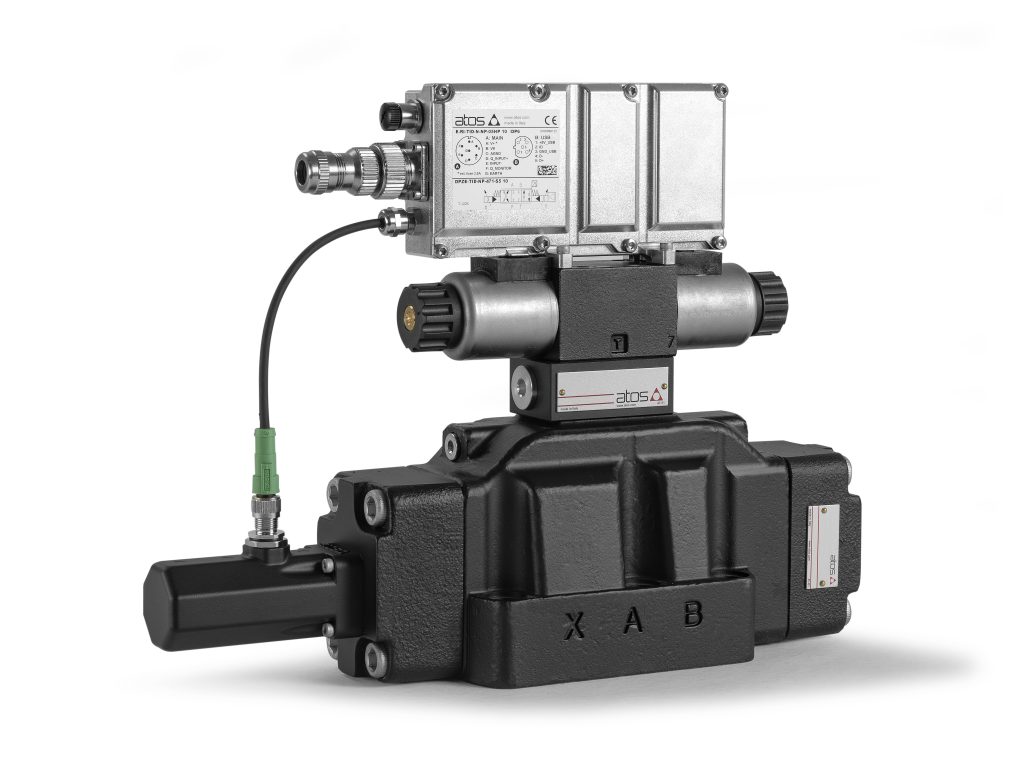
Optimized design
Efficient performances of the servopump, with the capability of reaching maximum rotation speeds of 3000 rpm, result also in the possibility of decreasing the sizes of the hydraulic unit. Through the angular position transducer integrated into the motor pump group, also the instantaneous flow rate is estimated with precision, as guarantee of higher accuracy and repeatability levels in comparison with proportional valves during flow rate control phases. Due to its high efficiency, the SSP system also allows the tank reduction and the removal of the heat exchanger, reaching higher rotation speeds. Everything leads to the reduction of the pump displacement. Great performances are scored also in noise levels. In comparison with a variable-displacement pump, the system developed by Atos reaches even 7dB less of sound emission during flow rate control phases and up to 20dB during pressure control ones, thanks to the low sound emissions of the gear pump and to the possibility of modulating the speed of the motor pump unit. Finally, with the integrated Multiple Axis function it is possible to select in real time the optimal parameters of the axes, maximising the performances of each machine motion. Through the S-SW-SIZING software, supplied free of charge, users can choose the most suitable servopump for their requirements simply, inputting the wished machine cycle. Moreover, the software can execute an energy estimate of the system, parametrizing the operational costs and the saving of CO2.
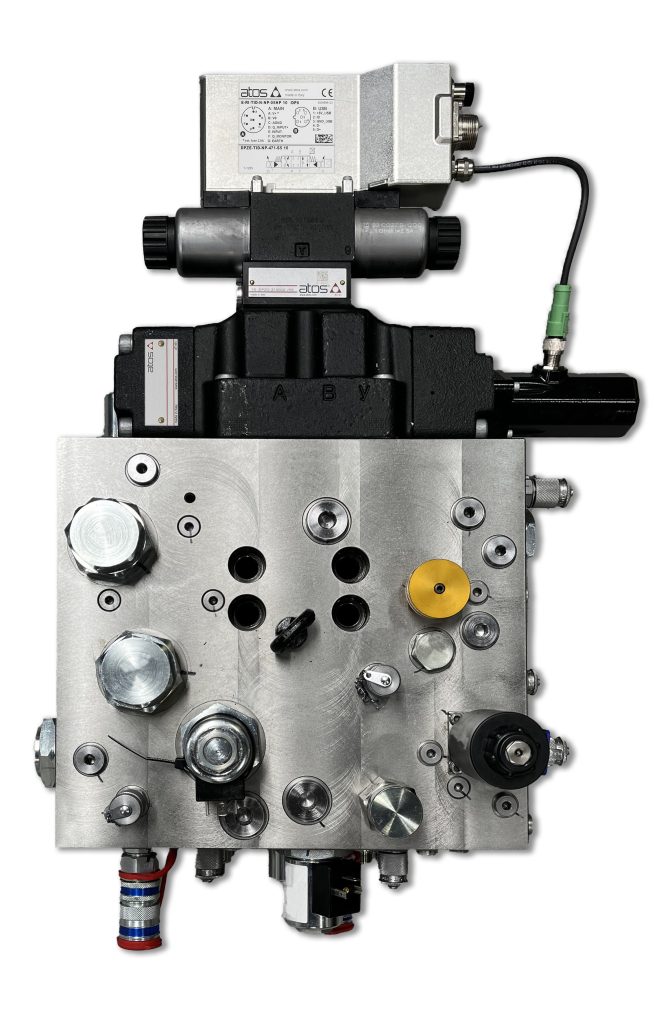
Proportional directional valves for wind turbines
Another solution developed by Atos to intercept the global boost towards sustainability aids in developing and exploiting alternative energy sources in comparison with those obtained from fossil fuels. It is the case of the core of proportional directional valves for wind turbines that represent the core of the hydraulic systems for the control of the blade pitch angle in the wind energy production. The hydraulic pitch control system modulates the keying angle of blades to control the generator speed with extreme precision, optimizing the energy production of turbines as response to the inconstant wind conditions. The range of valves developed by Atos for this sector represents an ideal choice, being designed to satisfy the strict requisites of onshore and offshore wind turbines, assuring an accurate control and high dynamics of the actuator position, combined with reliability and supported by advanced functions of configuration and diagnostics. The hydraulic system of pitch control is placed inside the turbine nacelle and allows making the three blades rotate to control precisely the speed of the base generator on a feedback signal.
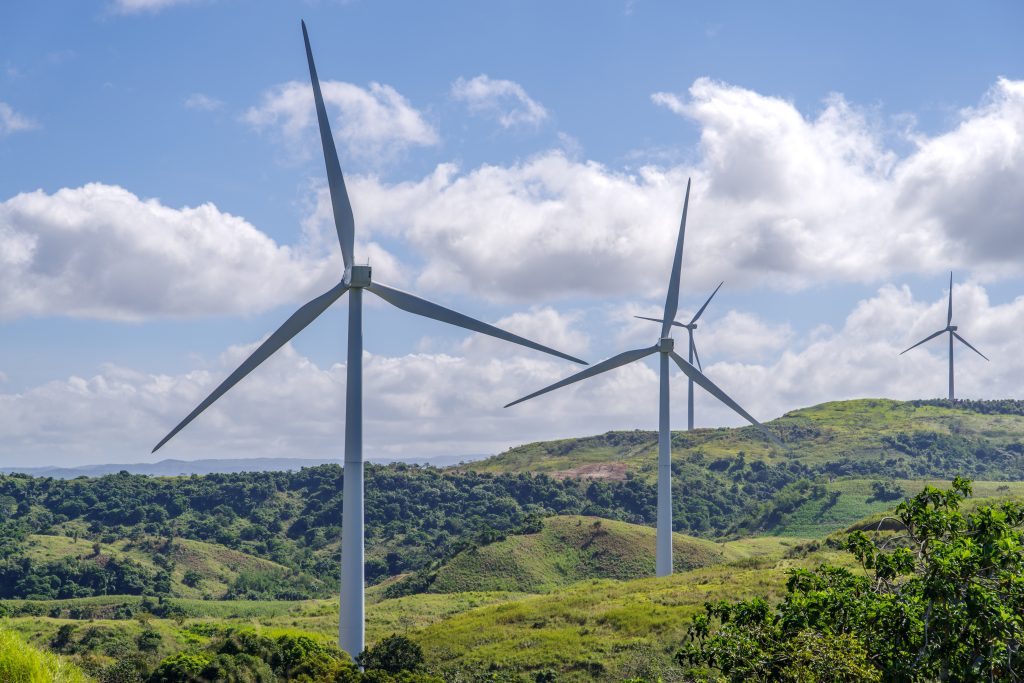
This process assures the production of the electric energy demanded irrespective of the variations of the wind speed, optimizing the energy efficiency and decreasing the mechanical load. In such way, also a prolonged service life of the wind turbine is assured. The reliability is another key factor of the system, owing to the high mechanical stresses affecting proportional directional valves, designed to operate under extremely critical conditions, like those of northern regions or in marine areas characterized by low temperatures and high wetness. Through the digital electronics, the valve performances can be optimized to satisfy the turbine requisites, in full compatibility with the existing control parameters.
Contacts:
Are you interested in hydraulic systems by Atos? Do not hesitate to contact Atos